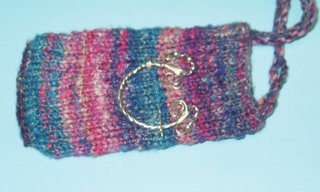
I love silk, and once in a while I just have to play! The above was the result of a weekend experiment. I dyed, spun and knitted a silk bell or cap into the cell phone cozy shown. It's the perfect size for carrying my cell around the office building where I work, and has enough extra room to tuck latte money inside as well!
Silk is the undisputed queen of fibers. No other fiber has the texture, sheen, strength and drape of silk, whether the fabric is woven, knitted, or knotted. Manmade fibers such as rayon, tencel, and soy are merely attempts to imitate what Mother Nature did with the Bombyx Mori moth – nice enough, to be sure, but still imitations.
In cost, silk is in the mid-range of fibers, with prices for silk top ranging from $40 to $75 per pound. Cocoons, bricks, and bells are less expensive, ranging between $2.50 and $5.50 per ounce. They are a wonderful option for many applications, including learning to spin this fabulous fiber.
Most spinners love to spin silk once they’ve tried it. We mix silk top in different proportions with all animal fibers and even cotton. Sock knitters mix silk with wool for strength and sheen. Weavers and knitters mix it with wool, alpaca and cashmere for the subtle sheen, unmatched drape and to stretch precious fibers. Dedicated cotton spinners mix it with dyed cotton lint to increase the shine and strength of their singles. Some spinners have made a lifetime study of silk in its many forms, spinning soft, textured yarns and harder, shiny ones. I’ve even heard of a couple of spinners who learned to spin by spinning silk!
First, let’s talk about the silk itself. Like most natural products, it comes in a variety of colors and qualities. Both color and quality depend upon the diet of the silkworms. Feed the worms low-quality foliage, and you will get low-quality silk, with weak spots and breaks in the length of the fiber. Feed the worms fresh, healthy mulberry leaves and you’ll get various shades of white cocoons, shiny and containing fine, strong fibers. Feed them different types of oak leaves and you’ll obtain various shades of tan and brown cocoons. Is there a science to the feeding? Of course. A good silk buyer can tell from the shade and quality of the cocoons where the silkworms were raised and whether there was adequate rainfall that season. Since they’ve done the hard part for us, we can simply concentrate on the shade of the fiber.
One caveat, however. If you’re tempted by a really good bargain in silk roving, check it carefully before you put down your hard-earned cash or plastic. Sometimes silkworms are fed a diet that is less than perfect, sometimes the weather is poor during their lifespan. This can result in fiber that is weak and brittle. Silk should be strong, requiring real muscle to break even a few of the short fibers in top or roving form. If you’re looking at bells or cocoons, see if the fibers are broken or if they appear to have thin spots. If the seller doesn’t want to allow you to inspect the silk, or if the color appears uneven, pass it by - it isn’t really a bargain.
Silk comes to spinners in several forms, as I mentioned above. Each has its uses for the fiber artist, so we’ll talk about each in turn. First are the cocoons themselves. You can dye them as cocoons with protein-fiber dyes, soak them for 24 hours in a crock-pot placed on low, pull the cocoons into a length and spin a very textured, heavy silk yarn. Beautiful as an accent yarn in any fabric. Of course, you have to remove the worm, but that isn’t really a problem.
You can reel and throw the silk yourself, which is a great deal of fun, but rather time-consuming. It does, however, make a beautiful, smooth yarn with all the best characteristics of the fiber. These yarns are perfect for weaving, lace-making, or knitting on very fine needles. A single ply (containing the unreeled fiber from 6 to 20 cocoons) can be plied with a single of another fiber for a mixed yarn with characteristics of both fibers. Directions for reeling silk are available in many locations, especially http://www.wormspit.com/.
The second form in which we buy silk fiber is that of a cap or handkerchief. These are fun, too. Silk caps are bell-shaped; handkerchiefs are square (just use the terms interchangeably – they’re the same thing except for the shape) and can be dyed with wool or protein fiber dyes as easily as wool. They will grab the color, giving brilliant results. After the cap is dry, separate it into single layers by inserting your hands into the center and snapping them apart several times around the circumference of the cap until it is loosened and fluffy. Then carefully pull the layers apart. Draw each layer out into a long, untwisted roving. You can wrap this around a paper roll or index card - a nostepinne works in a pinch, too. Then spin this “roving” or use it as is in a knitted or woven fabric. If you choose to use the roving unspun, be aware that the finished fabric will pick easily; a tight gauge will help with this.
The third form in which we purchase silk is probably the most common for spinners. That is silk roving or top. In order to produce this form, the reeled silk is cut into lengths varying from four to six inches. These cut lengths are then run through the same equipment that produces other fiber tops. The final product (prior to spinning) is a thick, unspun rope of aligned fibers. This is probably the easiest form of silk to blend with other fibers. If necessary, the fibers in the top can be cut into even shorter lengths to blend with shorter fibers like fine wools and cottons. While a cotton/silk blend is labor-intensive to produce by hand, it is beautiful in its final form. If doing it yourself doesn’t appeal, there are lovely painted rovings available from various sources.
Silk top forms a strong, slightly- to very-fuzzy yarn. The fuzziness will increase with wear. Why does a smooth fiber like silk turn fuzzy? Because the fibers in top have been cut to shorter lengths. Silk is a very smooth, slick fiber, with none of the scales and roughness associated with wools and bast plant fibers. When spun, these short ends escape the twist and create a halo effect in the yarn. This tendency can be used as a design element and enhanced by spinning the silk softly, which will increase the halo. The halo of soft-spun silk can approach that of angora or mohair. The spinner can also choose to minimize the halo by making very tightly-spun yarns with a great deal of twist. While these yarns will approach the appearance of reeled silk threads immediately after spinning, they will eventually halo as well (although not to the degree of the softer-spun yarns). The spinner is the designer here. Sample as necessary to create the yarn you want.
A little silk can go a long way. An ounce of silk will make anywhere from a hundred to a thousand yards of yarn. Again, the spinner determines the finished grist of the yarn. Some things to consider, though, are the final use of the yarn and the wear it will receive. My personal experience is that high-twist fine yarns show the sheen of the silk fiber best. These singles, with a grist usually between 60 and 100 wraps per inch, can be plied to whatever thickness is desired. These yarns are shiny and very strong, even in singles forms, as long as they have sufficient twist. Go back to your early days as a spinner when spinning silk. Twist is your friend, so use plenty of it! It takes a great deal of twist to keep the fibers in silk top from escaping. Twist also enhances the appearance of the silk yarn. So use your smallest whorl and treadle rapidly, or get out your lightest spindle and use lots of twist, adding even more than you think necessary. The finished yarn will be better for it.
I love to dye silk in any form. Spinning dyed silk caps, cocoons, or top is a pleasure. Silk is a protein fiber, so dyeing is simple. Silk dyes brilliantly with any wool dyes, commercial or natural, and you can obtain beautiful results with even simple dyes like food coloring and kool-aide. Mordants are simple as well - white vinegar or acetic acid give wonderful results. If you choose white vinegar, use approximately 1 cup per gallon of dye bath. If microwave or oven dyeing, simply soak the silk in the vinegar/water bath overnight before dyeing. Watch your temperature in the dye bath, however. Boiling water temperatures will cause the silk fibers to break down and weaken. So keep the dye bath at no more than 180 degrees Fahrenheit. Be sure to rinse your dyed fibers or yarns well, and a final rinse with some white vinegar added will neutralize any remaining dyes. Dry out of direct sunlight.
Silk and animal fiber blends are equally simple to dye. Just be sure to keep temperatures suited to the more delicate silk fibers. Silk-cotton blends are trickier. In home production, it’s usually best to dye the fibers separately and then combine them in the carding stage. The reason is simple. Cotton is a cellulose fiber that must be “scoured” and mordanted with often caustic chemicals in order to accept dyestuff. These mordants will destroy the silk fibers.
You can work around this, however. Silk is very reflective. It will blend well with dyed cottons with no dyeing itself. This makes it possible to blend silk with dyed cotton. Very fine silk singles can be plied with cotton and will almost disappear, with the eye focusing on only the dyed cotton color. You can also choose to dye only the silk, which will create a yarn with a tweedy or mottled effect, with the dyed silk showing as shiny flecks against the cotton. Or, as stated above, you can dye the silk separately and then combine the fibers. Again, spinner’s choice.
Treat all finished yarns and articles as though they were 100% silk. Silk care should consist of hand or very gentle machine washing in mild, neutral pH detergent. Following that with a vinegar rinse is recommended, too. Follow by flat or line drying and a cool iron if necessary. Silk is quite strong in mass, but individual fibers are delicate. The fine fibers will break down easily, and prolonged agitation or tumbling will hasten this process. Treated appropriately, however, silk is quite sturdy, with some of the fabrics lasting for generations. One additional note as to care is in order. Moths like silk as well as wool. So take precautions against infestation in both your finished articles and your fiber. Enjoy exploring the many facets of silk. It is, indeed, the queen of fibers, and will reward your efforts at understanding with many hours of spinning and wearing pleasure.
Details on the creation above? I dyed the silk cap with Wilton cake color in Delphinium, pre-soaking on Thursday night in a vinegar/water mixture and microwave dyeing on Friday after work. Saturday morning I pulled apart the silk cap, made it into a rough roving, and spun the layers into singles on a combination of spindle while I did errands and attended a guild meeting and wheel after I returned home. Sunday I plied the singles Navaho-fashion, mostly to preserve the lovely colorways. Twist in both singles and plies was quite high. The finished 3-ply yarn was between 15-18 wpi. I didn't even wash the yarn to set the twist - just cast on 39 stitches and immediately began a K2P1 ribbing, which I continued to the final four rows. I decreased 4 stitches every row on those last four rows, sock-toe fashion, switching to stockinette for those rows only. Finished up with a 3-needle bind-off to close the end, and made a three-ply cord of some of the remaining silk, stitching it to the top of the small purse with more of the silk.
The ribbing hugs the phone and, since it's about 2 inches longer than the phone itself, snuggles in above the phone to keep it in the purse. Yet when the phone rings, a simple squeeze at the bottom pops it out. The shawl pin decoration was an inspiration with a practical bent - I keep it in the office to wear with one of my shawls when the air conditioning gets to be too much and am constantly losing it in my desk drawer. This way I know exactly where it is when needed!