
What article of clothing is arguably most humble?
The “lowest” of all - the sock.
Eaten by dryers, mate-less cast aside, maligned by hurried owners,
Living in the rear of drawers and atop “to discard” piles,
Socks survive.
Stuffed into shoes, boots, and sandals,
Scuffed shoeless over floors, driveways, sidewalks and yards,
Tucked into gift boxes as a last-minute afterthought,
Maligned when absent, but needed,
Socks thrive!
Wool carefully chosen from saddle of fleece,
Lovingly washed, dyed, and combed,
Carefully spun smooth and strong, as carefully plied,
Knitted tightly, with heels expertly turned,
Gussets and toes decreased just so,
Socks pride!
From colors muted to startling bright,
From wools and cottons plain to silks and mohair boucléd.
In stitches simple and fancy, ribbings easy and hard,
Socks triumph!
Pamela Kite
December 19, 2003
Why on earth would anyone make socks from the sheep out? There are probably as many answers to that question as there are spinners and knitters who’ve ever done socks as a project. But some of those answers fall into distinct categories we can enumerate:
Socks require only about 4 ounces of fiber. That makes spinning for a pair a relatively short project, easily completed in a weekend or slightly more of precious spinning time.
For spinners with short attention spans, again 4 ounces (a single bobbin on most wheels) is a ‘doable’ amount. It doesn’t take forever to spin that amount, unlike spinning for a sweater, which can seem to take forever!
Spinners who have ‘dignified’ day jobs can let their jazzy side out to play with socks. Those who would never wear lacy, frilly things to work can wear lacy, frilly socks. They’re hidden beneath trousers, and almost never seen, but make the spinner feel secretly girly!
Socks are great sample projects for new fibers and spinning techniques. A couple of ounces of an exotic fiber you bought to play with can become a sock top, matched up with wool heels and feet for wear.
Socks are great for playing with color, too. The requirement isn’t all that great, either in terms of supplies or time, but you aren’t ‘wasting’ either – you’ll have a pair of socks to wear when you’re finished playing!
Handspun, handknitted socks can be designed for a specific wearer. Those of us who have feet that are an ‘odd’ size can fit ourselves and the specific tenderness of our feet precisely.
All right, these are some of the reasons you can have for spinning and knitting your own socks, or those for someone close to you. Now that we have that out of the way, let’s talk about sock history for just a second, and then get into how to choose a good fiber for the sort of sock we want to make and talk about some knitting guidelines for socks in general.
A Short Sock History
Foot coverings were originally called “leggings” and were wrapped lengths of fabric or hide. Wrappings didn’t like to stay put, though, and even tying string around them wasn’t a great deal of help. Then someone decided that foot coverings could be sewn from woven fabric. Seams generally went down the center of the top and bottom of the foot. These footlets were generally quite short – more or less anklets that could cushion wood or leather shoes, and are shown flopping over the tops of these shoes in paintings and drawings.
Sometime before the 5th century A.D., shaping legging fabrics to fit came into vogue. By 1500 feet were added to the leg covering, and ‘hose’ were sewn to fit each individual beginning around the same time. These were mostly for the wealthier members of society, however – peasants simply went barefoot or wore the short, floppy anklet versions.
Knitting was something of a revolution for sock-making. A fabric that actually could be made to stretch and fit more than one person! This was much too useful an innovation to be kept close in the European knitting guilds, and spread quickly. Now everyone with access to wool could have socks to help keep feet warm and cushion uncomfortable shoes!
Knitted, combined foot and leg coverings called stockings date back to at least the mid-1500’s, and quickly replaced sewn leg and foot coverings. By 1840, the term ‘sock’ had come to mean a man’s, boy’s or young girl’s foot and lower-leg covering.
Socks were a frequent first in-the-round knitting project for children. Comfortable socks are firmly knit, well-shaped fabrics, and making them with a neatly-turned heel was something of a milestone for young knitters, who then could go on to make more complicated pieces between seemingly endless pairs of socks. Sock-knitting was a more-or-less continual thing in families through the first half of the 20th century in less-developed areas of the world, including many areas of the United States. There are still areas of the world where the ability to knit stockings is considered a necessary skill.
Fiber Choices and Spinning Options for Socks
First, you can use any fiber to make a sock-shaped garment. Want to use singles superfine merino spun at 6 epi and knitted at 3 stitches per inch on size 6 needles? Go for it. Nobody will stop you. There are no spinning police and no knitting police. Enjoy wearing them, or hang them on a wall. They’ll definitely last longer on the wall, but again, wear them if you like. That, you see, is one of the benefits to doing it your way. You can do it your own way!
But if you want to spin for long-wearing, comfortable, warm socks that will keep their shape, choose a medium to medium-fine fleece like Romney or Border Leicester, Finn or Shetland – anything between 46 and 60 on the Bradford scale. Generally, you’ll choose a fleece for socks that is medium-soft, medium-long, and medium-crimpy. But if you go strictly by the breed characteristic you may neglect some good choices. I’ve spun Lincoln lamb with a count of 54, and it made wonderful, heavy sock yarn. Down breeds like Suffolk and Dorset are springy and almost impossible to felt. Some individual down fleeces are too coarse for anything but rugs, but some are perfect for socks! So don’t rule out ‘coarser’ or ‘meat’ fleeces until you check them personally. They may be exactly what you’re looking for!
You’ll definitely want to spin a worsted yarn – or as close to it as possible. For the best wear, yarns for socks should be made from aligned fibers, spun and compressed tightly. If you plan to choose fleeces with socks in mind, also plan to comb the fibers. With a medium fleece you can get away with a semi-worsted yarn – but worsted will wear better. In purchasing fibers for socks, look at top first. Leave the beautiful carded batts and rovings for sweaters and shawls and hats.
What I normally use in a class (or for my own socks) are three different fibers: first, a garden-variety domestic wool top with a Bradford count of 56; and second an 80/20 blend of wool and kid mohair top with a Bradford count of about 54. I also use small quantities of 64’s wool and silk in an 80/20 blend, also in a combed top preparation – lovely stuff, and at the outer realm of possibilities for socks, if spun quite carefully.
Start spinning the 56’s wool while we talk about some sock alternatives, both in fiber and spinning technique. For the newer spinners in the group, we’ll also touch on choosing and preparing raw fleeces. For now, set your spinning wheels in such a way that you can spin this 56’s wool to somewhere between 24-30 wpi singles. My suggestion is to start at a ratio of about 9:1, with light take-up. Aim for about 12 twists per inch in your finished singles. Tinker around with your wheel ratio and take-up until you get this grist. If you can spin it comfortably with a 6:1 ratio, that’s fine.
What grist [b]do[/b] you want to spin for sock yarn? It depends on the fleece. Socks will wear best if made from a tightly-spun yarn. But sometimes a single push of the treadle can make the difference between a firm yarn and a harsh one. I know you get tired of hearing ‘sample’ but you really do have to get over it. Look at sampling as shopping – you wouldn’t buy a soft-spun singles superfine merino wool for socks, so don’t spin one. Or look at sampling as exploration. You’re charting the potentialities of this particular fleece or top. However you look at or rationalize sampling, don’t neglect to do it. We learn by exploring.
Let’s talk about how fibers wear. Socks, in particular, wear mostly through friction – either the friction between the sock and the shoe, friction between the sock and the foot, or as a combination of those two. Some additional friction and temperature variation from the laundering process is also a contributing factor. The best way for a spinner to combat those sources of friction is to spin a firm, fairly high-twist yarn of multiple plies. Why? High-twist yarns are more compressed and have more twists per inch of each individual fiber than low-twist yarns. And the more plies you have, the less each individual fiber and ply are abraded and the better the wear.
Think back over your sock spinning and knitting experiences. Which yarns have given you the best wear? Which were almost indestructible? Was it the single-ply, low-twist, fine-fiber yarns, or the four-, five- or eight-ply yarns of wool and nylon or mohair?
I’m not suggesting that we try to hand-spin fingering-weight eight-ply merino blend yarns. Of course it can be done, and you may choose to do it at times, but it would tend to make those 4 ounces into a month’s rather than a weekend’s spinning. But 3- or 4-ply, even 4-ply cabled yarns are well within the realm of practicality for that hypothetical weekend. And they’ll give amazing wear from medium wools, and decent wear from fine wools.
My personal favorite sock yarns are cabled. Yes, I know I have to spin more singles yardage in order to cable the finished yarns. And I’m aware that I have to spin finer in order to end up with a sock-weight cabled yarn. But my knitting time is limited by the other things in my life. It’s much better in the long run to make socks that will last awhile, thus leaving more knitting time for things like sweaters and lace shawls and gloves and hats. My usual sock fleece or top is around 54-56 count. I haven’t found nylon to be particularly necessary in medium wools, although I have been known to blend it into the finer 58-62’s fibers. I usually spin this medium wool worsted-fashion at about 36 wpi as singles. This is not the time, however, for the smallest whorl on the wheel. I’ve learned that the best ratio for spinning this fiber firmly, without going over the line to harsh, is about 10:1. Yes, I sampled several fleeces and prepared tops to determine this. The socks are available for inspection whenever you want to drop by.
I spin the singles clockwise (Z), and ply the first time counterclockwise (S). Then I ply the resulting two-ply yarn again, clockwise. I end up with a nice sock-weight yarn of about 18 wpi and 10-14 tpi.
For the newbie spinner - What is a proper job of preparing a raw fleece for sock-spinning? There are all sorts of guidelines available online and in books, but simply put: First ruthlessly skirt and then clean the fleece. Process it for socks by combing, or by carding and removing the batts from the cards in such a way as to make a semi-worsted preparation. Spin it worsted-fashion with a high degree of twist to a grist of approximately 24-30 wpi. Two- or three-ply the singles, again with a fairly high degree of twist, to a finished yarn of about 16-18 wpi. Cable if desired.
I said earlier that you can use any fiber for making a sock-shaped garment, and that’s true. The alternatives for long-wearing, comfortable socks are a bit more limited, but there’s still plenty of leeway for the adventurous spinner-knitter. Let’s take a look at some of those alternatives to the norm, though, and why you might want to use them.
“I don’t like medium fibers – they’re scratchy and make my feet and ankles itch.” Sound familiar? It isn’t because the speaker’s being over-sensitive or unappreciative of your skills and talents – some people truly do find medium wools uncomfortable (my grandchildren included). So reclaim that pair for someone else and figure out another alternative. If medium wool’s too scratchy, can you make socks from finer wools? Sure you can! You can make socks from any fiber, remember?
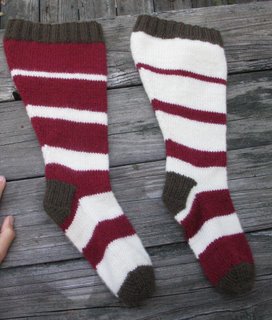
Softer fibers like merino, targhee, rambouillet and other merino crosses with Bradford counts in the 60’s can be used for socks with some thoughtful spinning and knitting modifications. You won’t get quite the wear from these that you will from a good Romney fleece, but they’ll be less prickly on tender feet and ankles. Blending these fine fibers with either tussah or bombyx silk will help wear, as will blending them with fine kid mohair or a bit of Lincoln or Wensleydale lamb fleece. Even ‘fake cashmere’ made from nylon will increase the wear for these fibers. And you can always blend some of that Romney or other medium-staple wool into the mix as well! Proportions will vary somewhat, but the usual recommendation is about 80 percent fine wool and 20 percent reinforcing fiber.
All right, you have that 80/20 blend. Now how should you spin it for decent wear and so that you don’t have to pull out the size 000 needles to knit the socks?
You’ll want to set up your wheel a little differently for fine fibers, of course, once you’ve zeroed in on the grist of singles and amount of twist you want. I usually go up a bit in speed when spinning finer fibers for socks. And you’ll definitely want a worsted preparation, which can be a bit tricky if you’re blending your own fibers – but persevere! If you want to try it, grab some 64’s merino blended with nylon or silk and set the wheel for a ratio of about 14 to 18:1. Set take up so it’s minimal – you want about 16-24 tpi on these singles. And try for singles in the 35-45 wpi range for a finished 4-ply cabled fingering-weight yarn.
You’ll want to use size 0 or 1 needles for these soft yarns to give better wear. If you’re a loose knitter, you may have to go to 00 needles. The idea is to counteract wear by knitting tightly. So aim for 8-12 stitches per inch. Swatch in the round until you have a very firm fabric with little or no movement in individual stitches. Check your gauge and figure your sock pattern accordingly. And remember, the idea here is wearability. Think process knitting. Even at 12 stitches per inch, most of us will have less than 100 stitches in a single round.
One last note on fine fibers: Plan to hand wash the socks carefully. And expect some felting with wear, especially on the bottom of the foot.
Now that we’ve talked about finer fibers for socks…Let’s talk about hand-painted tops for just a minute. They’re so gorgeous! How do you spin and ply to keep those lovely colors bright and unmuddied? You actually have two options, and variations within those options. Again, you’re in charge – make a choice and follow through!
Most commercially-painted top is made up of several colors, and the colors are blended in lengthwise stripes. Those stripes are pretty well-defined. It is possible to vertically strip each stripe apart and spin each strip as a different-color singles. You’ll have a few fibers in the neighboring color(s) in each strip, but they won’t show up enough to matter. Then ply the singles normally and knit as you would for any stripe pattern, changing the colors at the points of your choice.
All right, all right – I know this takes a lot of the fun out of things. You bought that top because you liked the way the colors flowed and blended. And it doesn’t help at all with the top or roving that you painted yourself in six- to ten-inch blocks of color! I did mention that there were at least two ways to spin multi-colored top, didn’t I?
For those color sections that are greater than the length of a single fiber you can, again, tear them apart and spin singles from each color, plying the singles and blending at the knitting stage. OR, you can spin them as they come (or after vertically pre-drafting a yard or more of the color changes for shorter color repeats), letting the colors fall where they may at the singles stage. Then Navaho-ply the singles slowly and carefully to make a three-ply yarn with beautiful color definition. Again, it’s up to you, the spinner. Learning Navaho-plying isn’t difficult, and the ‘bumps’ disappear in firmly-plied yarn. I’ve never felt a bump in my Navaho-plied socks, and I have pretty sensitive feet. If the Navaho-plied yarns are still gossamer-fine (possible if the top is a 64’s merino and silk blend), cable those yarns together for a thicker finished yarn.
The Knitting
When it’s time to knit, I choose needles that are about the same diameter as the yarn. That means 0’s, maybe 1’s, and only sometimes 2’s. That gives me a gauge of somewhere between 7 and 10 stitches per inch. You want a firm fabric for the same reasons that you do in finer wools – it will wear longer, with less pilling and felting. It will also feel better on the bottom of your feet – no uncomfortable rubbing of purl bumps after a couple of hours. You have to remember that you’re working with handspun – do a large (24-30 stitches and rows) circular gauge swatch and measure over at least 2 inches in at least 2 different places on the swatch. As spinners, our yarn is subject to some variation. As knitters, we can easily allow for that.
If you prefer to make toe-up socks, a gauge swatch is still a valuable reference, as it can keep you from having to frog and re-work the toe cast-on several times. You can start out with the needles that give you the fabric you want. Remember, you need a firm fabric.
The other variable is fit. You can check the previous reference on this blog for fit hints. But socks that slide around on your foot will require much more extensive and frequent darning than those that fit closely, regardless of the fiber you’ve chosen. Socks, in case you haven’t already figured this out, require negative ease. For those who haven’t run across this term before, I’ll explain briefly.
When you’re making a sweater, you want to add anywhere from 5 to 18 percent of your skin-level circumference in order to arrive at your finished dimensions. In addition to ease, this is because sweater fabric is thick, taking up some room (up to three inches total in bulky yarns), and sweaters insulate better if they aren’t skin-tight. Socks, on the other hand, need to be skin-tight in order to provide the cushioning your foot requires without taking up too much room in your shoe or sliding around as you walk. So you want your sock fabric to be slightly stretched during wear. My own rule of thumb is to subtract an inch’s worth of stitches from the circumference. In other words, a 10-inch circumference will require 9 inches worth of knitting. Another suggestion is to subtract 20 percent from your as-measured circumference to arrive at a cast-on number.
In Closing
Your mother probably told you that everybody is different, and she was right. Every sheep is different, too. While there are general breed characteristics that mean you probably wouldn’t choose Lincoln or Churro for a baby layette, there are also exceptions to the standard. Shepherds can and do breed for softness, fineness, crimp or luster in their flocks. And cross-bred sheep can show the best of several ‘parent’ breeds. My favorite sock yarns come from Shetland-Romney crosses that belong to a friend.
If you follow the above instructions you [b]will[/b] make well-fitting, long-wearing socks from your handspun.
What about making socks from luxury fibers? I really haven’t tried much of that. I did put angora cuffs on a pair of socks – the angora felted long before the wool, and I had to cut it off and re-knit the cuffs from wool. I made one pair of socks (at my father-in-law’s request) from a 50-50 wool-yearling mohair blend. He loves them, and is still wearing them six years later. But I thought then and still think that the fabric is just too scratchy! My next experiment (when I get around to it) will probably include some alpaca, simply because I’m on an alpaca ‘kick’ lately. But right now I’m happy sticking to wool for my socks.